To analyze and improve a (business) process, you need to first know what is going on in it. In other words, your job is to map the process.
26.10.2023
Heikki Immonen, Karelia University of Applied Sciences
A map is a simplified model of reality. It allows you to see the order of things – which actions lead to what results and other actions. It helps you to see the bigger picture, while at the same time focusing on details. Most importantly, process improvement and analysis become much easier, when the processes are mapped out.
- Some studies say that many business performance indicators improve by up to 50 % as a result of applying lean improvement strategies where process mapping plays a key role.
In the simplest terms, process mapping is about defining each step in the process and then defining the resources and tools used in each step.
Let’s look at both of these steps in detail.
Define each process step
To define each step in a process, do as follows:
- Zoom out and define the boundaries of the overall process you are studying and the transformation that happens as a result of the process.
- Zoom in and walk through the process step by step.
- For each step, define and document the transformation that happened as a result of the process step.
- Check for consistency
Zooming out and defining the boundaries
Zooming out and defining the boundaries of the process you are studying puts limits on what you are trying to map. Zooming out means that you see your process as a single big process step. When you define the transformation that happens as a result of it, you end up defining the boundaries of it, too.
To describe one big or small process step, you can use the following template: process name: input à output. Here, the input à output defines the transformation the process is responsible for. For example:
- Cake-baking: flour + water + sugar + eggs à cake
- App marketing: audience who has not heard of the app à customers who have paid and installed the app
Or use a table format like this:
Process name | Input | Output |
Cake-baking | flour, water, sugar, eggs | cake |
App marketing | audience who has not heard of the app | customers who have paid and installed the app |
The input and output states define the overall boundaries of the out-zoomed process you are studying.
Zoom in and walk through the process step by step
Next step is to zoom into the process. This happens by starting from the input state and walking through the whole process until you reach the output state. If your process is already in action, walking through means that you follow each step and make observations.
If the process you want to map is something you have not implemented yet, you need to imagine all the steps needed. If you have past experience of similar processes, it will be relatively easy to simulate or model the process based on your experience.
TIP. AI can be helpful in sketching the process you are mapping. To do this, you can simply describe the process you are studying and describe the input and output states. Then ask the AI to sketch out the subprocesses or process steps.
As a result of this step, you will have a list of intermediary process steps. For example,
- Cake baking steps:
- Ingredient preparation
- Mixing
- Preparing the baking pan
- Baking
- Cooling
- Frosting and decorating
For each step, define and document the transformation that happened as a result of the process step
Third, for each process step, define and document the transformation that happened as a result of the process step. This step works exactly the same as you did with the zoomed-out process. To define the transformation, you simply need to define the input and output state of the process step.
For example:
- Preparing the baking pan: Empty cake pan + butter à greased cake pan
You should list the process steps in chronological order. Use numbering, for example. If the process steps are parallel, meaning that they can happen at the same time, you can visualize them as parallel, or separate them with letters.
In this example, we highlight a couple of process steps that can be done in parallel. For the sake of clarity, we have excluded the input and output states:
- Cake baking steps:
- Ingredient preparation
- Mixing
- Preparing the baking pan
- Baking
- Cooling & preparing the frosting
- Cooling the cake
- Preparing the frosting
- Frosting and decorating
Lists like the one above are useful, but there are also several ways you can prepare your process for better inspection.
- Map the process in a spreadsheet
- Create a flowchart
- Draw the process using pen & paper
Check for internal consistency
Finally, check for internal consistency of your process map. To do this, you compare the output state of each process step with the input state of the following process. Everything is good, if everything seems logical.
TIP: AI can help you define the input and output states. Ask the AI to exclude equipment and tools. Look at the answer AI gives you to see if it made any mistakes. On the other hand, AI can look at the mapping you made and see if there are any mistakes there.
Define the resources needed for the next step
After you have mapped each process step, it is time to focus on the resources needed in the process. There are two types main types of resources:
- Consumable resources
- Non-consumable resources
Consumable resources
Consumable resources are literally consumed or somehow irreversibly transformed in the process. Actually, when you define each process step using the input and output state, you were already defining most of the consumable resources needed. However, you should be clear of what the initial resources in the beginning of the process that are consumed (or irreversibly transformed) as a result of the process.
For example:
- Cake baking consumable resources:
- From the process step analysis: flour, water, sugar, eggs, butter, cream
- Not mentioned in the process step analysis: energy (electricity)
Non-consumable resources
Non-consumable resources are the equipment, tools, people, skills and methods needed to handle each process step. They are not consumed or destroyed in the process, but can be reused time after time.
- When a business invests in something, it means that it is buying (acquiring) non-consumable resources.
If the process you are analyzing already exists, finding out what the non-consumable resources are, is easy. If you are still in a planning stage, it might not be clear which tool or method you want to use to handle a specific step. Don’t worry! Since you have defined the process steps early without the non-consumable resources (as the input and output states), it is now very easy to ask for external help and search for the most suitable options.
Here are some examples of [non-consumable resources] needed in various processes:
- Cake baking [oven]
- App marketing [social media]
- Gardening [hand shovel]
- App developing [code editor]
- Shoe selling [online store]
As told earlier, skills, methods and knowledge are all non-consumable resources, too. They are also non-physical, i.e. informatical resources.
Here is an example of few process steps of cake-baking process along with the non-consumable resources used in the process.
Process step | Resources (non-consumable) | Input | Output |
Preheating the oven | oven | oven in room temperature | oven in 200 °C |
Baking | oven | cake batter in pan, oven in 200 °C | baked cake (hot) |
Cooling | baked cake (hot) | baked cake (cool) | |
Frosting | cream mixer, pastry decorating tube | baked cake (cool), cream | frosted cake |
About this article
The writing of this article was supported by the INnoVations of REgional Sustainability: European UniversiTy Alliance project. https://www.invest-alliance.eu/ . This project is funded by the Erasmus+ Program.
The content of this article represents the views of the author only and is his sole responsibility. The European Commission and the Agency do not accept any responsibility for use that may be made of the information it contains.
References
Anthony, S. D. (2014). The first mile: A launch manual for getting great ideas into the market. Harvard Business Review Press.
Bicheno, J., & Holweg, M. (2016). The Lean Toolbox 5th Edition: A Handbook for Lean Transformation. PICSIE Books.
Dori, D. (2016). Model-based systems engineering with OPM and SysML (Vol. 15). Springer.
Immonen, H. (2021). Application of object-process methodology in the study of entrepreneurship programs in higher education.
Liker, J. K. (2021). Toyota way: 14 management principles from the world’s greatest manufacturer. McGraw-Hill Education.
Miller, D., & Peterson, J. J. (2020). Marketing made simple: A step-by-step storybrand guide for any business. HarperCollins Leadership.
Siegenfeld, A. F., & Bar-Yam, Y. (2020). An introduction to complex systems science and its applications. Complexity, 2020, 1-16.
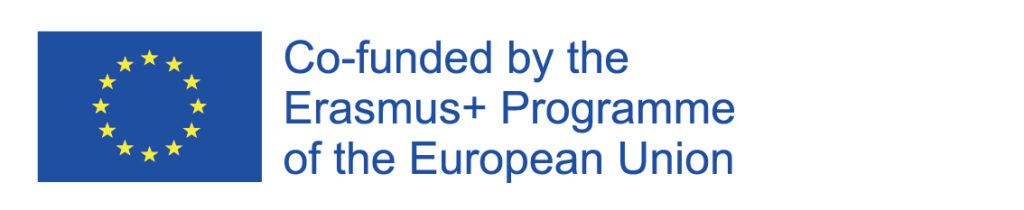
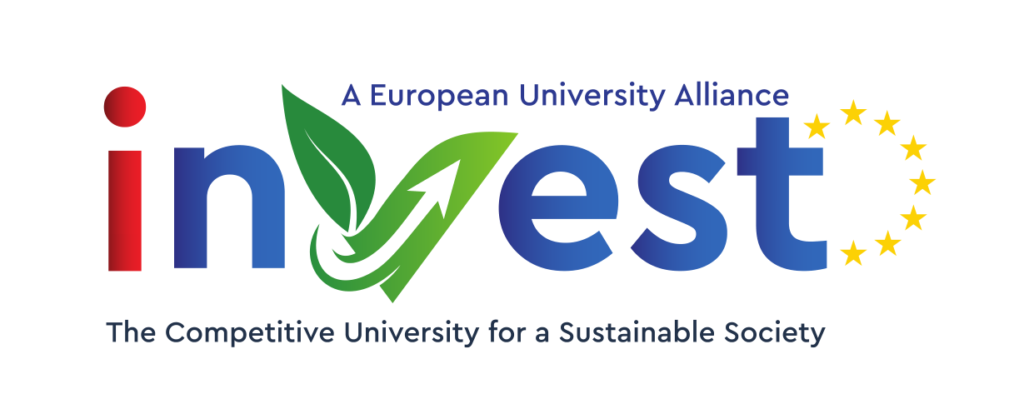