Analysis and improvement of the processes of your business is one of the most valuable things you can do to increase the likelihood of the success of your business.
26.10.2023
Heikki Immonen, Karelia University of Applied Sciences
If you have created a map of your the process of your business, like the one below, you can study it. (Find a quick guide for doing process mapping here)
Process step | Resources (non-consumable) | Input | Output |
Preheating the oven | oven | oven in room temperature | oven in 200 °C |
Baking | oven | cake batter in pan, oven in 200 °C | baked cake (hot) |
Cooling | baked cake (hot) | baked cake (cool) | |
Frosting | cream mixer, pastry decorating tube | baked cake (cool), cream | frosted cake |
Studying the process can then lead to improvements. When analyzing a process, there are several types of questions you can ask:
- How much time does each process step take?
- What resources are we lacking?
- Is our process wasteful?
Let’s look at each of these in more detail.
How much time does each process step take?
A process is a transformation and all transformations take time. (Someone might go as far as saying that time IS transformation). In business, and in life, time is a scarce consumable and an expensive resource. That is why you need to carefully look at how you are spending it.
If the process you are studying already exists, you can take a watch and measure the time spent. If the process you are studying does not exist yet, you need to estimate the time spent to the best of your knowledge. Write the durations for each step next to the corresponding process step.
If your process map is in a table format, it could look something like this after adding the durations of each process step:
Process step | Resources (non-consumable) | Input | Output | Duration |
Preheating the oven | oven | oven in room temperature | oven in 200 °C | 12 min |
Baking | oven | cake batter in pan, oven in 200 °C | baked cake (hot) | 35 min |
Cooling | baked cake (hot) | baked cake (cool) | 40 min | |
Frosting | cream mixer, pastry decorating tube | baked cake (cool), cream | frosted cake | 8 min |
TOTAL | 95 min |
When you have the information about how long it takes to do each step, you will immediately get insights.
- You can think if some process steps could be done faster.
- You can also estimate how much time it takes to make a different number of your product or serve multiple customers.
If you are paying yourself or someone else to handle the process, you can now more realistically estimate the total profitability of your business. For example,
- Based on her profitability calculation, she knows that her cake business needs to sell 866 cakes annually in order for her to reach her profit goal and her desired 50 % part-time salary. If the total cake baking time per cake is 2 hours she is in trouble. This would mean that she needs 2 h/cake * 866 cakes = 1732 hours to bake her cakes. This is bad because she is only paying herself a 50 % part-time salary, which is roughly 800 hours per year. Luckily, she can do many things to fix this. For example, she can design a smarter and faster process with multiple cakes being baked at the same time.
To learn more about these types of calculations, check out this article that introduces reverse income statement, a startup-oriented way to do profitability analysis.
What resources are you lacking?
You can use a process map to see what tools, equipment, skills or knowledge you are still missing. This is especially important for a new startup company who is still in the process of building up their processes.
If you are combining the process step analysis with profitability analysis, you suddenly have a simulation of your business process. You can calculate how many inputs each process step needs to have each day and how many outputs you need to produce.
With the process map and the accompanying analysis, you can only invest in the resources you actually need. External investors appreciate and require you showing them how their money will be invested in things that really matter.
For companies that are already established and growing, the process map is also a very valuable tool when planning the recruitment of new employees. The process map helps to clarify very clearly which process steps the new employee needs to handle and with which tools.
Is our process wasteful?
Finally, a process map is a powerful tool for removing waste. This becomes relevant when the startup business has started to do the first test runs of the new process.
When your map and the analysis is detailed enough, you will be able to spot activities and process steps that are unnecessary. Common examples of these types of unnecessary activities are:
- Searching for something needed to complete a process step. Solution: learn to return tools and resources needed on their dedicated spot.
- Unnecessary movement. Moving back-and-forth in a storage to get the required things. Solution: re-organize things so that everything is easily and readily accessible.
- Quality problems cause rework and fixing. Solution: specify the quality problem causing process step and improve the step by removing the cause of the problems.
- Waiting. Solution: analyze the process and recognize the process step that is the bottleneck. Improve the throughput of your whole process by improving this single slowest process step.
In summary, a process map makes the analysis and improvement of your business processes easier. It helps you to see the big picture while it also allows you to focus on each individual step.
About this article
The writing of this article was supported by the INnoVations of REgional Sustainability: European UniversiTy Alliance project. https://www.invest-alliance.eu/ . This project is funded by the Erasmus+ Program.
The content of this article represents the views of the author only and is his sole responsibility. The European Commission and the Agency do not accept any responsibility for use that may be made of the information it contains.
References
Anthony, S. D. (2014). The first mile: A launch manual for getting great ideas into the market. Harvard Business Review Press.
Bicheno, J., & Holweg, M. (2016). The Lean Toolbox 5th Edition: A Handbook for Lean Transformation. PICSIE Books.
Dori, D. (2016). Model-based systems engineering with OPM and SysML (Vol. 15). Springer.
Immonen, H. (2021). Application of object-process methodology in the study of entrepreneurship programs in higher education.
Liker, J. K. (2021). Toyota way: 14 management principles from the world’s greatest manufacturer. McGraw-Hill Education.
Miller, D., & Peterson, J. J. (2020). Marketing made simple: A step-by-step storybrand guide for any business. HarperCollins Leadership.
Siegenfeld, A. F., & Bar-Yam, Y. (2020). An introduction to complex systems science and its applications. Complexity, 2020, 1-16.
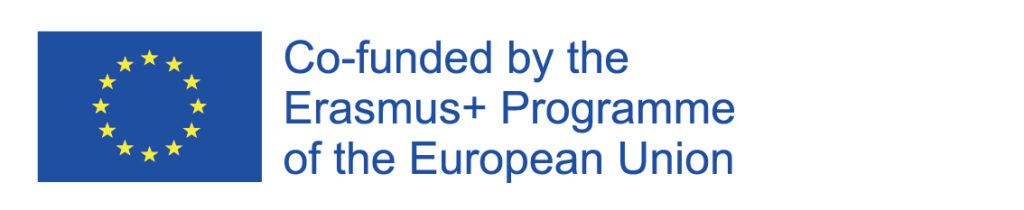
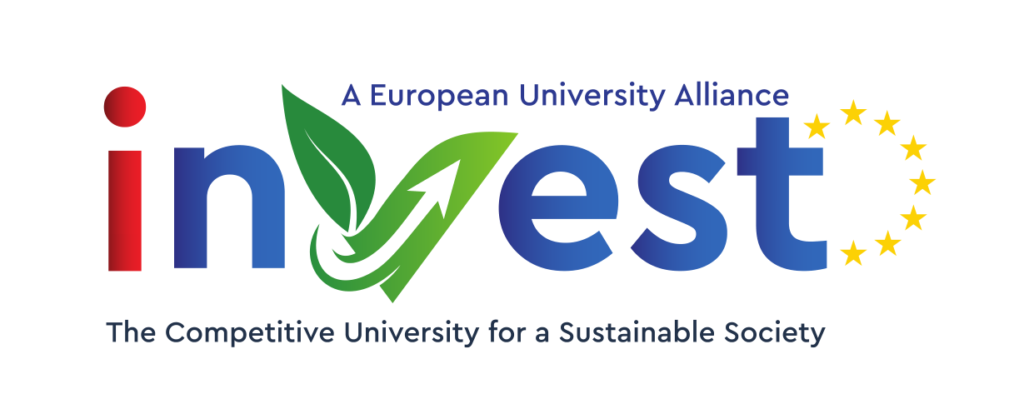